Parker Square: Design Flexibility, Streamlined Construction Process using Custom Manufacturing
Parker Square is a community touch point with a unique collection of independent businesses, vibrant restaurants and personal services. The architect for the project envisioned detailed cast stone cladding work that highlights artistic brick veneer patterns on the building facade. The AAS team custom engineered stone to realize architect’s design intent of making it look as if large brackets on top corners of building sides are bearing weight of the projecting cornice bands.
Project: Parker Square, Flower Mound, Texas
Architect: Dulaso & Associates, LLC
Masonry Contractor: Artisan Masonry
Product: Cast Stone
AAS capabilities used for project specific custom stone manufacturing:
- Design Assist – Detailed review of CAD drawings early in the project lifecycle to confirm design feasibility.
- Fabrication of molds for a range of stone shapes and sizes – the CNC technology enabled precise control over tolerances, eliminating visually disruptive discontinuities between stone panels.
- Pre-engineering and thorough detailing of connections for hanging the manufactured stone panels.
- Developing a very specific custom color using specific admixture developed in the in-house color lab, and consistently matching that color for every single cast stone piece used in the project using the fully automated computerized batch plant.
- Rigorous testing to verify color and structural properties of the manufactured stone pieces.
- Construction Assist – Close collaboration, communication with customer to match manufacturing schedule with construction milestones. The AAS team answered questions about specific installation details.
COORDINATION OF LARGE BRACKETS AND CORNICE BANDS
The design intent from architect was to have the appearance that the upper cornice band was solely supported by the massive projecting brackets.
For the precise matching of the brackets with the cornice band, the AAS engineering team developed molds with custom shapes. Each cornice piece is hung using the band strap anchors.
Project specific stone manufacturing:
- Early in the design phase of the project, the AAS team pre-engineered anchorage connections to hang brackets and cornice panels, and confirmed those with the client.
- With direct translation of the CAD drawing details into CNC machine programming, the fabricated molds met stringent tolerance requirements precisely.
- Where required, AAS was able to cast both sides of the stone panels. This is an advantage with the dry vibrant-tamp casting technique.
The visual continuity between cornice bands and brackets achieved the design intent of this feature.
HIGHLIGHTING DETAILED BRICK WORK PATTERNS
The architect extensively used the cast stone to bring attention to the very detailed brick patterns and details.
The AAS system to precisely design and fabricate stone pieces with specific shapes, enabled smooth execution of the project without delay in construction. The installation team got detailed settings plan that identified placement of every stone piece used in the project. Detailed CAD drawings for different sections clearly described how to hang the stone panels.
The architect selected a custom color that required a specialized sand that required a blending to satisfy ASTM C1364 requirements.
CAST STONE BASE, DOOR AND WINDOW TRIM STIMULATES STORE FRONTS
The cast stone base, window and door trim with projecting lintels stimulates the storefront features.
CONSTRUCTION COORDINATION, PROJECT PLANNING, CUSTOMER SUPPORT
- The AAS team provided settings plan along with fully automated tracking system to identify and track every single stone piece used in the project. (Image below shows example settings plan for the northeast elevation of the building).
- Staging, sequencing, palletization and delivery of manufactured stone in batches to simplify planning at the construction site.
- Training to explain connection details for hanging stone pieces used in the project, onsite troubleshooting.

Parker Square Northeast Elevation Settings Plan
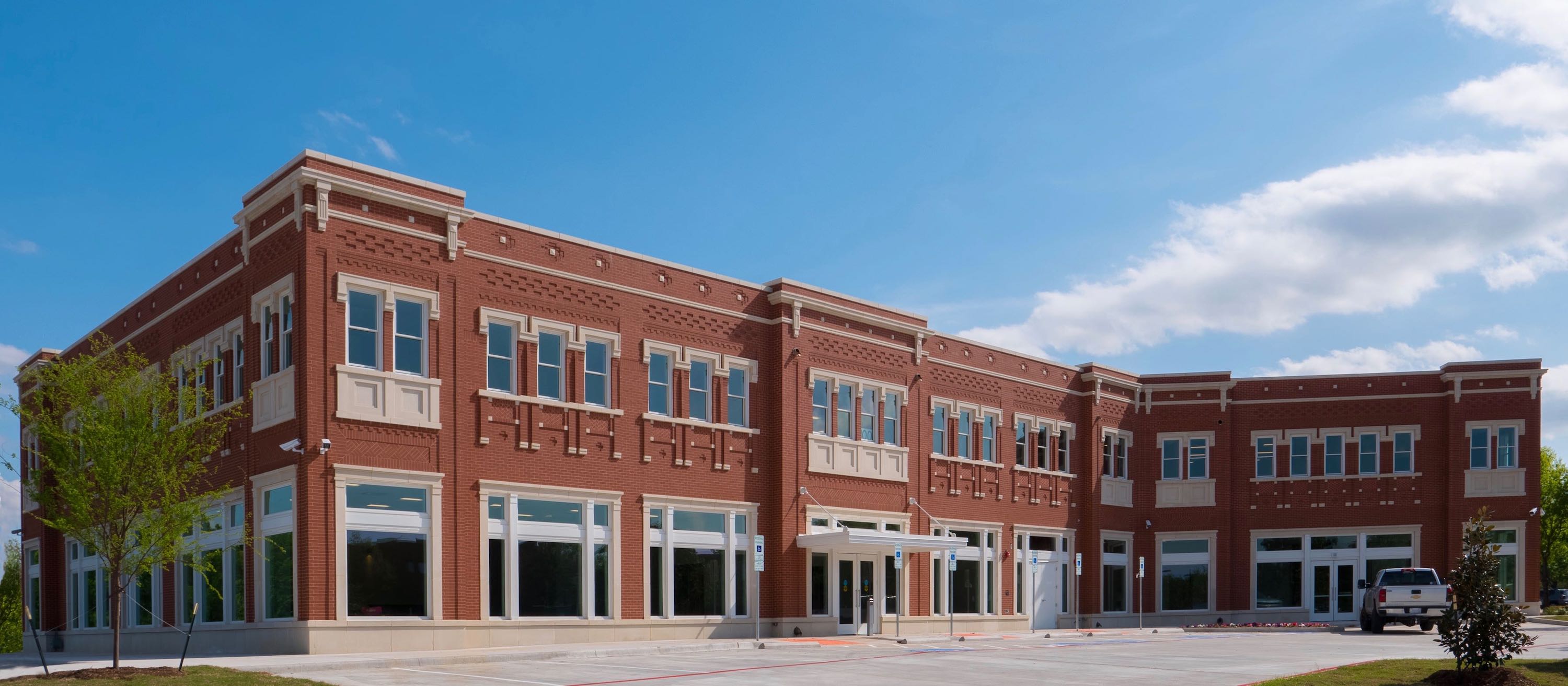
Parker Square Project | AAS Cast Stone Cladding | Entry way, door and window trim, cornices, banding, large brackets