The new ROTC building at University of Central Florida highlights a 13-sided sculpture honoring our country and soldiers throughout the history.
The AAS team created framed views of the sculpture using architectural cast stone panels. The sculpture is housed in a one and half feet thick rotunda made from custom design dry-cast stone, and GFRC concrete panels. The rotunda is three stories high with 30 feet in diameter. There are three large radius openings in it with a complex series of step backs that create framed views of the sculpture from different directions.
This three-dimensional frame accentuates and emphasizes the unique sculpture symbolizing the spirit and storied tradition of the ROTC.
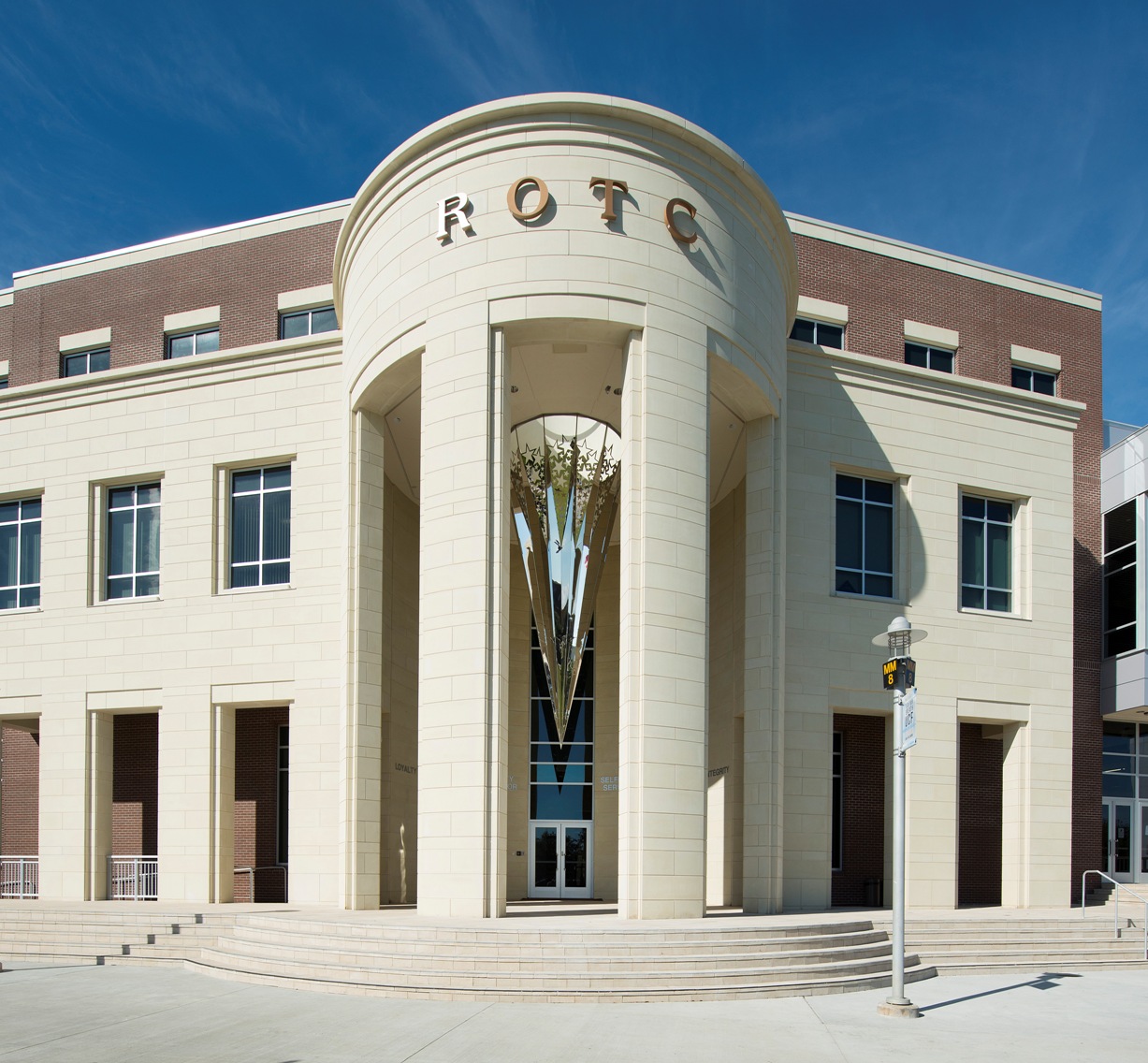
AAS Project : ROTC Classroom at University of Central Florida | Architectural Stone Created Design of 3-Dimensional Frame for the Unique Sculpture
Color and texture consistency of architectural stone was achieved through a computer driven batch design.
The CNC technology was utilized to design custom molds for the GFRC, cast stone wall panel pieces. Every one of the manufactured stone wall panels matched extremely stringent tolerance requirements. With all stone panels seamlessly fitting together, the entrance facade achieved desired look of a monolithic piece of stone.
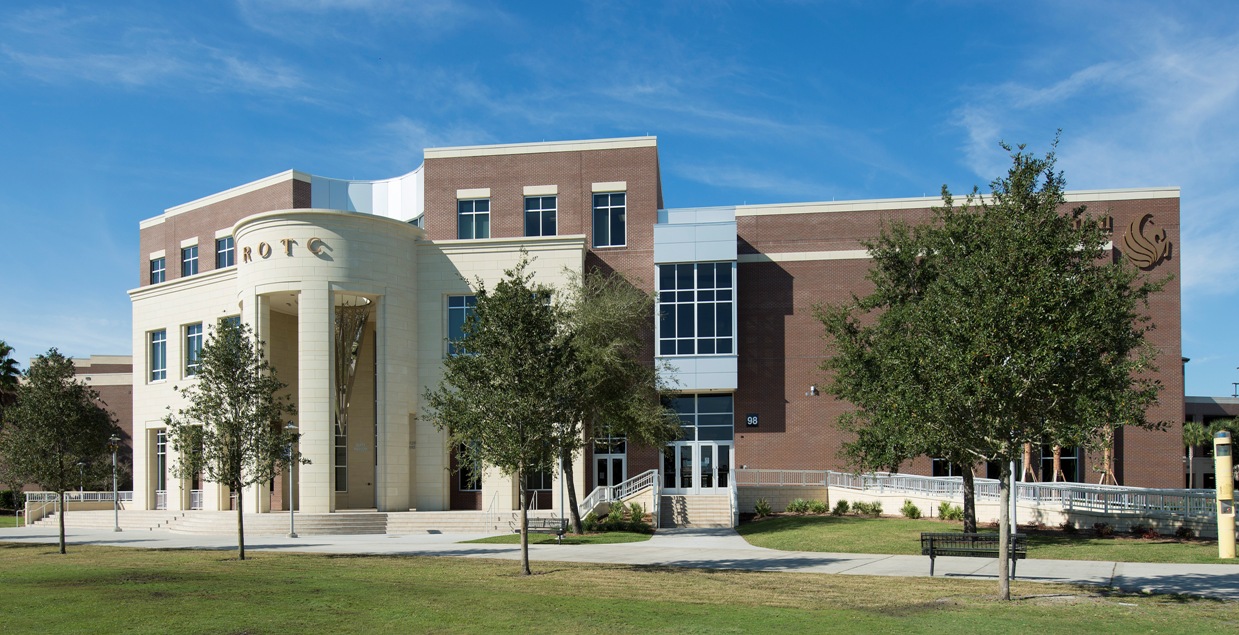
University of Central Florida ROTC Classroom II Building | Architectural Stone Design Created Monolithic Look for the building facade | Stone Veneer
Exterior Veneer using Manufactured Stone Panels
The front entry and exterior of the building has architectural stone veneer that played a key role in harmonizing the new building with the rest of the school campus.
The facade veneer combined three different types of stone veneer panels – thin lightweight GFRC (Glass Fiber Reinforced Concrete) panels at the higher elevation, vibrant-tamp architectural dry cast stone for the framing and cladding design elements, as well as wet-precast architectural concrete where stronger structural support was required.
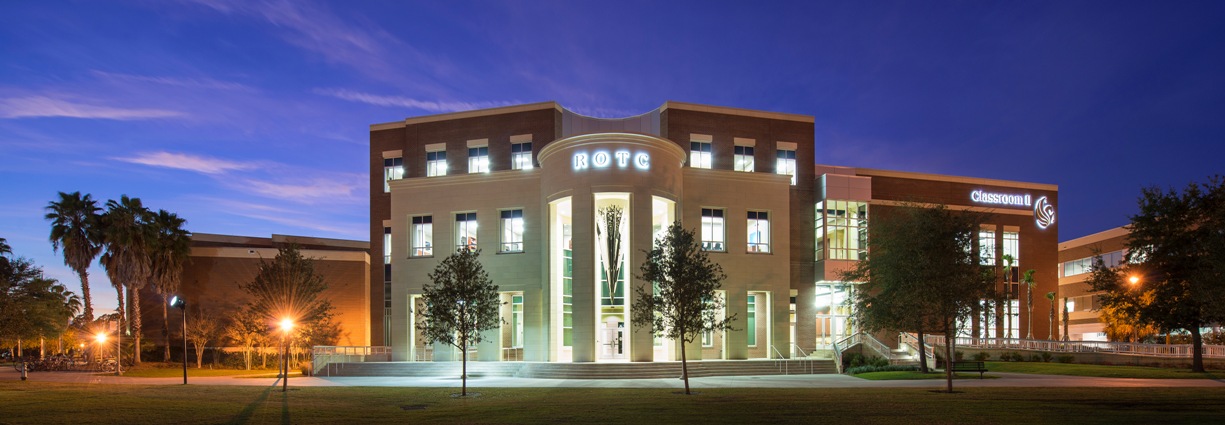
AAS Formerly ACS | Architectural Stone Veneer, Cladding Harmonized new ROTC Building with campus of University of Central Florida (UCF)
Project Name: University of Central Florida Classroom Building II ROTC
Architect: Schenkel Shultz, Architecture/Interior Design
General Contractor: Clancy & Theys Construction
Products Used: GFRC, Architectural Cast Stone, as well as Architectural Precast Concrete
VENEER, FACADE DESIGN USING FABRICATED STONE PANELS: MORE PROJECT EXAMPLES, LEARN MORE >>
ARCHITECTURAL STONE CLADDING: SEE MORE PROJECT EXAMPLES, LEARN MORE >>